This is one of the world’s leading suppliers of rigid plastics packaging products and plastic containers. They have 89 manufacturing sites 18 design and engineering centres in 24 countries, employing 15,000 people.
The initial heat recovery assessment highlighted the potential energy savings available. UAP then carried out the full design and installation of the heat recovery system, providing a complete turnkey solution.
What is Heat Recovery?
Heat recovery is the collection and re-use of heat arising from any process that would otherwise be lost!
Some common uses for heat recovery include:
- Pre-heating Boilers, Ovens, Furnaces.
- Hot water Generation.
- Space Heating.
- And many more.
The customer was using gas boilers to heat the office space in their building in Chester. By installing plate heat exchangers to all the air compressors on site and specific regulating valves, we were able to provide and maintain a supply of hot water at a constant 70°C temperature.
By utilising our bespoke low loss header design, any heat and energy losses were significantly reduced. In addition, our low loss header improves the longevity of the heat recovery system by distributing an even temperature throughout the system and reducing the risk of thermal shock.
Recovering the waste heat from the compressed air system on site, the customer was able to heat their offices at a constant temperature. This allowed for the boilers to be completely switched off, reducing their energy consumption and carbon footprint.
with a payback period of only 6 months!
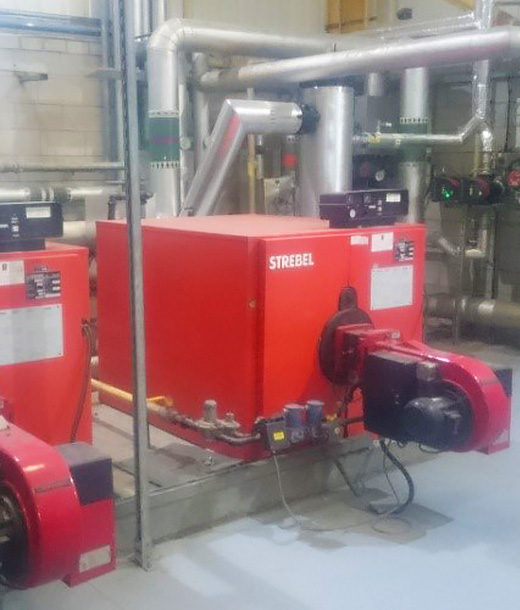
I was really impressed with UAP’s professional approach and commitment to helping us meet our energy efficiency targets. UAP designed and installed the heat recovery system to our compressed air system, which eliminated our annual gas consumption by 76,744 litres, and saved us £47,466.16 per annum. The environment also benefited from a reduction of 97,236.40kg per annum of harmful carbon emissions released into the UK’s atmosphere, by needless heat generation.
Engineering Manager